冲击铆机
Impact riveting is an assembly process using impact force to permanently fasten components together. There exist a wide variety of rivet materials, rivet designs, and component types which can be assembled using the impact riveting process to join parts quickly, efficiently, and lastingly.
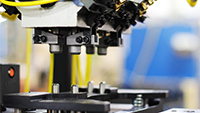
- 型号
- HP-2000
- R-2000
- RHV-2000

The Orbitform HP-2000 impact riveting machine is a hydraulic-pneumatic pedestal riveter tooled to feed and set one rivet at a time. This air-over-oil riveter, which over feeds the rivet and provides for upset, curl or stake to be formed conventionally by lower tooling, can set a wide range of solid or semi-tubular rivets. The riveter can form solid mild steel rivets up to .437" (11.1 mm) diameter. The quiet operation of the machine makes for an operator friendly work environment while the few moving parts keep the riveter maintenance friendly. Typical applications include heavy duty assembly operations such as automotive seat tracks, truck frame components, and metal bed frame assemblies.
Max Rivet Diameter | .437" (11.1 mm) |
Max Rivet Length | 1.5" (38.1 mm) |
Throat Depth | 18.0" (457.2 mm) |
Max Stroke | 4.0" (101.6 mm) |
- Download .dwg
- Download .easm
- Download .step
Orbitform’s HP-2000 impact riveter is manufactured and assembled at Orbitform’s factory in Jackson, Michigan, USA. The air over oil impact riveting machine is available with many standard features and the impact assembly machine can be customized with options to help monitor, control, and improve the assembly process. Orbitform’s application engineers listen and seek the appropriate answer for each specific assembly process being considered. Orbitform’s team can outline the required upper and lower tooling to conduct the riveting application and, if the customer desires, Orbitform can design and build turnkey assembly machines complete with machine actuation, safety system, fixturing method, error proofing process, and/or other expert assembly features associated with impact riveting machines and automatic assembly equipment.
The incredibly robust design of this hydraulic-pneumatic riveting machine results in machines operating for 50 or more years in continual service. The riveter's fabricated frame, base, and lower tooling support arm offer the strength required for the most demanding solid rivet and semi-tubular riveting applications in the world. As with all Orbitform riveting machines, the Model HP-2000 is constructed to insure many years of continuous productivity and is designed to accept modifications to accommodate special needs.
Standard Impact Rivet Machine Features and Specifications
- 10.0” diameter air actuated hopper to store rivets to be automatically released to the machine
- Machine actuation: Standard unit shipped with guarded footswitch with air cylinder operated clutch
- Tooling: (1) set of engineered-to-suit tooling is included (Jaws / Driver / Rollset)
Impact Rivet Machine Options:
Electrical Options:
- PLC machine control with dual palm button actuation
- Dual opto-touch actuation upgrade (requires a part holding fixture) to allow for lower effort operator actuation
Mechanical Options:
- Probe type safety device to disable the machine if there are any obstructions in the rivet setting area
- Spare tooling package (Jaws / Drivers / Rollsets) to supplement the tooling that comes standard with the machine
- Vibratory hopper upgrade so the machine can hold additional rivets or if the rivets have a feature precluding the standard hopper bowl feeding method
- Part holding fixture to support the components prior to riveting
- Narrow Anvil Arm w/steel insert (customer part defined)
- Altered lower rollset holder (customer part defined)
- Tonnage Monitor to precisely determine the force being applied
- Four (4) leveling pads to keep the riveting machine level on uneven surfaces

The Orbitform Model R-2000 impact riveting machine is a single-drive, electro-mechanical pedestal riveter tooled to feed and set one rivet at a time. This riveter, which over feeds the rivet and provides for upset, curl or stake to be formed conventionally by lower tooling, can set a wide range of solid or semi-tubular rivets. The riveter can form solid mild steel rivets up to .250" (6.35 mm) diameter as effortlessly as small .089" (2.26 mm) aluminum semi-tubular rivets as a result of the Model R-2000's six tons of setting force. Typical applications include automotive seat tracks, tail pipe hanger assemblies, drum cover rings, garden tools and metal bed frame assemblies.
Max Rivet Diameter | .25" (6.35MM) |
Max Rivet Length | 2.0" (50.8 mm) |
Throat Depth | 8" - 12" (202 mm - 304 mm) |
Max Stroke | 5.0" (127 mm) |
- Download .dwg
- Download .easm
- Download .step
Orbitform’s Model R-2000 impact riveter is manufactured and assembled at Orbitform’s factory in Jackson, Michigan, USA. The impact riveting machine is available with many standard features and the impact assembly machine can be customized with options to help monitor, control, and improve the assembly process. Orbitform’s application engineers listen and seek the appropriate answer for each specific assembly process being considered. Orbitform’s team can outline the required upper and lower tooling to conduct the riveting application and, if the customer desires, Orbitform can design and build turnkey assembly machines complete with machine actuation, safety system, fixturing method, error proofing process, and/or other expert assembly features associated with impact riveting machines and automatic assembly equipment.
The robust design of this riveting machine results in machines operating for 50 or more years in continual service. The riveter's column, base, and frame offer the strength required for the most demanding solid rivet and semi-tubular riveting applications in the world.The Model R-2000 muscle is transmitted through a toggle arrangement which delivers the force as a controlled squeeze. The Model R-2000 features a non-repeat clutch and is easily retooled. As with all Orbitform riveting machines, the Model R-2000 is constructed to insure many years of continuous productivity and is designed to accept modifications to accommodate special needs.
Standard Impact Rivet Machine Features and Specifications
- 10.0” diameter air actuated hopper to store rivets to be automatically released to the machine
- Machine actuation: Standard unit shipped with guarded footswitch with air cylinder operated clutch
- Tooling: (1) set of engineered-to-suit tooling is included (Jaws / Driver / Rollset)
Impact Rivet Machine Options:
Electrical Options:
- PLC machine control with dual palm button actuation
- Dual opto-touch actuation upgrade (requires a part holding fixture) to allow for lower effort operator actuation
Mechanical Options:
- Probe type safety device to disable the machine if there are any obstructions in the rivet setting area
- Spare tooling package (Jaws / Drivers / Rollsets) to supplement the tooling that comes standard with the machine
- Vibratory hopper upgrade so the machine can hold additional rivets or if the rivets have a feature precluding the standard hopper bowl feeding method
- 10" diameter mechanical hopper upgrade so the machine can hold additional rivets or if the rivets have a feature precluding the standard hopper bowl feeding method
- Part holding fixture to support the components prior to riveting
- Narrow Anvil Arm w/steel insert (customer part defined)
- Altered lower rollset holder (customer part defined)
- Tonnage Monitor to precisely determine the force being applied
- Available with 8" - 12" (202 mm - 304 mm) throat depth for applications where the part being assembled is large
- Four (4) leveling pads to keep the riveting machine level on uneven surfaces

The Orbitform Model RHV-2000 impact riveting machine is a single-drive, electro-mechanical pedestal riveter tooled to feed and set one rivet at a time. This riveter, which over feeds the rivet and provides for upset, curl or stake to be formed conventionally by lower tooling, can set a wide range of solid or semi-tubular rivets. The riveter can form solid mild steel rivets up to 0.375" (9.5 mm) diameter as a result of the Model RHV-2000's 15 tons of setting force. Typical applications include automotive seat tracks, automotive fans, window regulator assemblies, gear housings, farm machinery components, bed frames and heavy-duty hand tools.
Max Rivet Diameter | .437" (11.1 mm) |
Max Rivet Length | 1.5" (38.1 mm) |
Throat Depth | 8" - 12" (202 mm - 304 mm) |
Max Stroke | 5.0" (127 mm) |
- Download .dwg
- Download .easm
- Download .step
Orbitform’s Model RHV-2000 impact riveter is manufactured and assembled at Orbitform’s factory in Jackson, Michigan, USA. The impact riveting machine is available with many standard features and the impact assembly machine can be customized with options to help monitor, control, and improve the assembly process. Orbitform’s application engineers listen and seek the appropriate answer for each specific assembly process being considered. Orbitform’s team can outline the required upper and lower tooling to conduct the riveting application and, if the customer desires, Orbitform can design and build turnkey assembly machines complete with machine actuation, safety system, fixturing method, error proofing process, and/or other expert assembly features associated with impact riveting machines and automatic assembly equipment.
The robust design of this riveting machine results in machines operating for 50 or more years in continual service. The riveter's column, base, and frame offer the strength required for the most demanding solid rivet or semi-tubular riveting applications in the world.
The Model RHV-2000 muscle is transmitted through a toggle arrangement which delivers the force as a controlled squeeze. The Model RHV-2000 features a non-repeat clutch and is easily retooled. As with all Orbitform riveting machines, the Model RHV-2000 is constructed to insure many years of continuous productivity and is designed to accept modifications to accommodate special needs.
Standard Impact Rivet Machine Features and Specifications
- 10.0” diameter air actuated hopper to store rivets to be automatically released to the machine
- Machine actuation: Standard unit shipped with guarded footswitch with air cylinder operated clutch
- Tooling: (1) set of engineered-to-suit tooling is included (Jaws / Driver / Rollset)
Impact Rivet Machine Options:
Electrical Options:
- PLC machine control with dual palm button actuation
- Dual opto-touch actuation upgrade (requires a part holding fixture) to allow for lower effort operator actuation
Mechanical Options:
- Probe type safety device to disable the machine if there are any obstructions in the rivet setting area
- Spare tooling package (Jaws / Drivers / Rollsets) to supplement the tooling that comes standard with the machine
- Vibratory hopper upgrade so the machine can hold additional rivets or if the rivets have a feature precluding the standard hopper bowl feeding method
- Part holding fixture to support the components prior to riveting
- Narrow Anvil Arm w/steel insert (customer part defined)
- Altered lower rollset holder (customer part defined)
- Tonnage Monitor to precisely determine the force being applied
- Available with 8" - 12" (202 mm - 304 mm) throat depth for applications where the part being assembled is large
- Four (4) leveling pads to keep the riveting machine level on uneven surfaces