冲击铆机
Impact riveting is an assembly process using impact force to permanently fasten components together. There exist a wide variety of rivet materials, rivet designs, and component types which can be assembled using the impact riveting process to join parts quickly, efficiently, and lastingly.
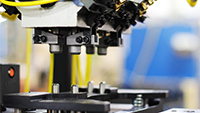
- 型号
- Milford 56
- Milford 57
- Milford 58
- Milford 63
- Milford 64
- Milford 255
- Milford 256
- Milford 305
- Milford 310
- Milford 313
- Milford 405
- Milford 410
- Milford 413
- Milford 423

The Milford Model 56 impact riveter is a pneumatically driven modular riveting head, tooled to automatically feed and set one (1) rivet per cycle. This unit is specifically designed for integration with automated assembly equipment, and is well suited for applications requiring single or multiple riveters. The space saving wedge design permits grouping of two or more units as close as 1.0" (25.4 mm) on a common base. The standard unit is supplied without controls, but controls may be supplied as a complete turn-key system if you select the optional bench-top base and controls package. The impact riveting units are commonly used with automotive window molding assemblies, instrument panels, appliance components, electrical devices, brake shoes, and other light duty riveting processes. The cushion squeezing riveting action lends itself to applications such as clinching of rivets through plastic, ceramic and other relatively brittle materials.
Max Rivet Diameter | 0.125" (3.2mm) |
Max Rivet Length | 0.562" (14.3mm) |
Stroke | 2.0" (50.8mm) |
Weight | 90 Lb |
Throat Depth | 9.0" (229mm) |
- Download .eprt
- Download .step
Orbitform’s modular Milford Model 56 impact riveter is manufactured and assembled at Orbitform’s factory in Jackson, Michigan, USA. The impact riveting machine is available with many standard features and the impact assembly machine can be customized with options to help monitor, control, and improve the assembly process. Orbitform’s application engineers listen and seek the appropriate answer for each specific assembly process being considered. Orbitform’s team can outline the required upper and lower tooling to conduct the riveting application and, if the customer desires, Orbitform can design and build turnkey assembly machines complete with machine actuation, safety system, fixturing method, error proofing process, and/or other expert assembly features associated with impact riveting machines and automatic assembly equipment.
Standard Impact Rivet Machine Features and Specifications
- 2" diameter bore x 2" long stroke pneumatic cylinder
- 5.25” diameter rotary mechanical hopper to store rivets to be automatically released to the machine
- Machine actuation: Standard unit shipped without controls
- Tooling: (1) set of engineered-to-suit tooling is included (Jaws / Driver / Rollset)
Impact Rivet Machine Options:
Electrical Options:
- Controls package with footswitch actuation to allow the machine to be cycled by the operator’s foot so the operator can support he workpiece in his/her hands
- PLC machine control with dual palm button actuation
- Dual opto-touch actuation upgrade (requires the selection of the bench-top base assembly) to allow for lower effort operator actuation
Mechanical Options:
- Probe type safety device to disable the machine if there are any obstructions in the rivet setting area
- Spare tooling package (Jaws / Drivers / Rollsets) to supplement the tooling that comes standard with the machine
- Bench-top base assembly (including controls package with footswitch and rollset holder) to allow for a complete bench-top rivet setting assembly machine
- Pedestal assembly (including controls package with footswitch and rollset holder) to allow for a complete floor standing rivet setting assembly machine
- Custom machine table designed and built to optimize the customer’s assembly process
- Quick Change raceway with one (1) set of tooling (Jaws / Driver / Rollset) to allow the riveting machine to be adapted to a different rivet size
- Vibratory hopper upgrade so the machine can hold additional rivets or if the rivets have a feature precluding the standard hopper bowl feeding method
- Load deflection device
- Part holding fixture to support the components prior to riveting
- Pilot operated check valve to allow for pressure relief
- Toggle bar maintenance tool (Orbitorm item number AC-296) to allow the machine to be manually cycled for process set-up and testing
- Offset driver package for limited clearance space assembly applications
- Load cell link pin to be used in conjunction with an operator interface panel (HMI) to display rivet setting forces

Orbitform’s modular Milford Model 57 impact riveter is manufactured and assembled at Orbitform’s factory in Jackson, Michigan, USA. The impact riveting machine is available with many standard features and the impact assembly machine can be customized with options to help monitor, control, and improve the assembly process. Orbitform’s application engineers listen and seek the appropriate answer for each specific assembly process being considered. Orbitform’s team can outline the required upper and lower tooling to conduct the riveting application and, if the customer desires, Orbitform can design and build turnkey assembly machines complete with machine actuation, safety system, fixturing method, error proofing process, and/or other expert assembly features associated with impact riveting machines and automatic assembly equipment.
Max Rivet Diameter | .187" (4.75 mm) |
Max Rivet Length | .75" (19.0 mm) |
Stroke | 3.0" (75.05mm) |
Weight | 230 lbs (104.5 kg) |
Throat Depth | 12.0" (304.5mm) |
- Download .eprt
- Download .step
The Milford Model 57 impact riveter is a pneumatically driven modular riveting head, tooled to automatically feed and set one (1) rivet per cycle. This riveting unit is designed for integration with automatic assembly machinery, and is well suited for applications requiring single or multiple riveters. The space saving wedge design permits grouping of two or more units as close as 1.00" (25.4 mm) on a common base. The standard unit is supplied without controls, but controls may be supplied creating a turn-key assembly system if you select the optional bench-top base and controls package, the pedestal assembly, or a custom machine. The impact riveting units are commonly used with automotive window molding assemblies, instrument panels, appliance components, electrical devices, brake shoes, and other light duty riveting processes. The cushion squeezing riveting action lends itself to applications such as clinching of rivets through plastic, ceramic and other relatively brittle materials.
Standard Impact Rivet Machine Features and Specifications
- 3" diameter bore x 4" long stroke pneumatic cylinder
- 7.5” diameter rotary mechanical hopper to store rivets to be automatically released to the machine
- Machine actuation: Standard unit shipped without controls
- Tooling: (1) set of engineered-to-suit tooling is included (Jaws / Driver / Rollset)
Impact Rivet Machine Options:
Electrical Options:
- Controls package with footswitch actuation to allow the machine to be cycled by the operator’s foot so the operator can support he workpiece in his/her hands
- PLC machine control with dual palm button actuation
- Dual opto-touch actuation upgrade (requires the selection of the bench-top base assembly) to allow for lower effort operator actuation
Mechanical Options:
- Probe type safety device to disable the machine if there are any obstructions in the rivet setting area
- Spare tooling package (Jaws / Drivers / Rollsets) to supplement the tooling that comes standard with the machine
- Bench-top base assembly (including controls package with footswitch and rollset holder) to allow for a complete bench-top rivet setting assembly machine
- Pedestal assembly (including controls package with footswitch and rollset holder) to allow for a complete floor standing rivet setting assembly machine
- Custom machine table designed and built to optimize the customer’s assembly process
- Quick Change raceway with one (1) set of tooling (Jaws / Driver / Rollset) to allow the riveting machine to be adapted to a different rivet size
- Vibratory hopper upgrade so the machine can hold additional rivets or if the rivets have a feature precluding the standard hopper bowl feeding method
- Load deflection device
- Part holding fixture to support the components prior to riveting
- Pilot operated check valve to allow for pressure relief
- Toggle bar maintenance tool (Orbitorm item number AC-296) to allow the machine to be manually cycled for process set-up and testing
- Offset driver package for limited clearance space assembly applications
- Load cell link pin to be used in conjunction with an operator interface panel (HMI) to display rivet setting forces

The Milford Model 58 impact riveter is a pneumatically driven modular riveting head, tooled to automatically feed and set one (1) rivet per cycle. This unit is specifically designed for integration with automated assembly equipment, and is well suited for applications requiring single or multiple riveters. The standard space saving wedge design permits grouping of two or more units as close as 1.0" (25.4 mm) apart or as close as 0.750" (19 mm) with our off set driver model. The standard unit is supplied without controls, but controls may be supplied as a complete turn-key system if you select the optional bench-top base and controls package. The impact riveting units are commonly used with automotive window molding assemblies, instrument panels, appliance components, electrical devices, brake shoes, and other light duty riveting processes. The cushion squeezing riveting action lends itself to applications such as clinching of rivets through plastic, ceramic and other relatively brittle materials.
Max Rivet Diameter | .25" (6.5 mm) |
Max Rivet Length | .75" (19.0mm) |
Stroke | 3.0" (76.25mm) |
Weight | 230 lbs (104.5 kg) |
Throat Depth | 12.0" (304.5mm) |
- Download .eprt
- Download .step
Orbitform’s modular Milford Model 58 impact riveter is manufactured and assembled at Orbitform’s factory in Jackson, Michigan, USA. The impact riveting machine is available with many standard features and the impact assembly machine can be customized with options to help monitor, control, and improve the assembly process. Orbitform’s application engineers listen and seek the appropriate answer for each specific assembly process being considered. Orbitform’s team can outline the required upper and lower tooling to conduct the riveting application and, if the customer desires, Orbitform can design and build turnkey assembly machines complete with machine actuation, safety system, fixturing method, error proofing process, and/or other expert assembly features associated with impact riveting machines and automatic assembly equipment.
Standard Impact Rivet Machine Features and Specifications
- 3-1/4" diameter bore x 4" long stroke pneumatic cylinder
- 7.5” diameter rotary mechanical hopper to store rivets to be automatically released to the machine
- Machine actuation: Standard unit shipped without controls
- Tooling: (1) set of engineered-to-suit tooling is included (Jaws / Driver / Rollset)
Impact Rivet Machine Options:
Electrical Options:
- Controls package with footswitch actuation to allow the machine to be cycled by the operator’s foot so the operator can support he workpiece in his/her hands
- PLC machine control with dual palm button actuation
- Dual opto-touch actuation upgrade (requires the selection of the bench-top base assembly) to allow for lower effort operator actuation
Mechanical Options:
- Probe type safety device to disable the machine if there are any obstructions in the rivet setting area
- Spare tooling package (Jaws / Drivers / Rollsets) to supplement the tooling that comes standard with the machine
- Bench-top base assembly (including controls package with footswitch and rollset holder) to allow for a complete bench-top rivet setting assembly machine
- Pedestal assembly (including controls package with footswitch and rollset holder) to allow for a complete floor standing rivet setting assembly machine
- Custom machine table designed and built to optimize the customer’s assembly process
- Quick Change raceway with one (1) set of tooling (Jaws / Driver / Rollset) to allow the riveting machine to be adapted to a different rivet size
- Vibratory hopper upgrade so the machine can hold additional rivets or if the rivets have a feature precluding the standard hopper bowl feeding method
- Load deflection device
- Part holding fixture to support the components prior to riveting
- Pilot operated check valve to allow for pressure relief
- Toggle bar maintenance tool (Orbitorm item number AC-296) to allow the machine to be manually cycled for process set-up and testing
- Offset driver package for limited clearance space assembly applications
- Load cell link pin to be used in conjunction with an operator interface panel (HMI) to display rivet setting forces

The Milford Model 63 impact riveter is an electro-mechanical, flywheel driven bench-top riveting machine, tooled to automatically feed and set one (1) rivet per cycle. This unit is specifically designed for operator loaded assembly applications. This single spindle riveter will automatically feed and set one semi-tubular rivet per cycle. Our standard unit comes equipped with a 120 volt motor, and controls for footswitch actuation. Typical applications for this model riveter include HVAC assemblies, hinged assemblies, furniture components, appliance components, electrical devices, brake shoes, etc.
Max Rivet Diameter | .093" (2.25mm) |
Max Rivet Length | .562" (14.25mm) |
Stroke | 2.0" (50.75mm) |
Weight | 235 lbs (106.5 kg) |
Throat Depth | 6.25" (158.75mm) |
- Download .eprt
- Download .step
Orbitform’s modular Milford Model 63 impact riveter is manufactured and assembled at Orbitform’s factory in Jackson, Michigan, USA. The impact riveting machine is available with many standard features and the impact assembly machine can be customized with options to help monitor, control, and improve the assembly process. Orbitform’s application engineers listen and seek the appropriate answer for each specific assembly process being considered. Orbitform’s team can outline the required upper and lower tooling to conduct the riveting application and, if the customer desires, Orbitform can design and build turnkey assembly machines complete with machine actuation, safety system, fixturing method, error proofing process, and/or other expert assembly features associated with impact riveting machines and automatic assembly equipment.
Standard Impact Rivet Machine Features and Specifications
- 5.25” diameter rotary mechanical hopper to store rivets to be automatically released to the machine
- Machine actuation: Standard unit shipped with guarded footswitch
- Tooling: (1) set of engineered-to-suit tooling is included (Jaws / Driver / Rollset)
Impact Rivet Machine Options:
Electrical Options:
- Controls package with footswitch actuation to allow the machine to be cycled by the operator’s foot so the operator can support he workpiece in his/her hands
- PLC machine control with dual palm button actuation
- Dual opto-touch actuation upgrade (requires the selection of the bench-top base assembly) to allow for lower effort operator actuation
Mechanical Options:
- Probe type safety device to disable the machine if there are any obstructions in the rivet setting area
- Spare tooling package (Jaws / Drivers / Rollsets) to supplement the tooling that comes standard with the machine
- Bench-top base assembly (including controls package with footswitch and rollset holder) to allow for a complete bench-top rivet setting assembly machine
- Pedestal assembly (including controls package with footswitch and rollset holder) to allow for a complete floor standing rivet setting assembly machine
- Custom machine table designed and built to optimize the customer’s assembly process
- Quick Change raceway with one (1) set of tooling (Jaws / Driver / Rollset) to allow the riveting machine to be adapted to a different rivet size
- Vibratory hopper upgrade so the machine can hold additional rivets or if the rivets have a feature precluding the standard hopper bowl feeding method
- Load deflection device
- Part holding fixture to support the components prior to riveting
- Narrow Anvil Arm w/steel insert (customer part defined)

The Milford Model 64 impact riveter is an electro-mechanical, flywheel driven bench-top riveting machine, tooled to automatically feed and set one (1) rivet per cycle. This unit is specifically designed for operator loaded assembly applications. This single spindle riveter will automatically feed and set one semi-tubular rivet per cycle. Our standard unit comes equipped with a 120 volt motor, and controls for footswitch actuation. Typical applications for this model riveter include HVAC assemblies, hinged assemblies, furniture components, appliance components, electrical devices, brake shoes, etc.
Max Rivet Diameter | .156" (4.0 mm) |
Max Rivet Length | .75" (19 mm) |
Stroke | 2.0" (50.75 mm) |
Weight | 235 lbs (106.5 kg) |
Throat Depth | 6.25" (158.75 mm) |
- Download .eprt
- Download .step
Orbitform’s modular Milford Model 64 impact riveter is manufactured and assembled at Orbitform’s factory in Jackson, Michigan, USA. The impact riveting machine is available with many standard features and the impact assembly machine can be customized with options to help monitor, control, and improve the assembly process. Orbitform’s application engineers listen and seek the appropriate answer for each specific assembly process being considered. Orbitform’s team can outline the required upper and lower tooling to conduct the riveting application and, if the customer desires, Orbitform can design and build turnkey assembly machines complete with machine actuation, safety system, fixturing method, error proofing process, and/or other expert assembly features associated with impact riveting machines and automatic assembly equipment.
Standard Impact Rivet Machine Features and Specifications
- 7.5” diameter rotary mechanical hopper to store rivets to be automatically released to the machine
- Machine actuation: Standard unit shipped with guarded footswitch
- Tooling: (1) set of engineered-to-suit tooling is included (Jaws / Driver / Rollset)
Impact Rivet Machine Options:
Electrical Options:
- Controls package with footswitch actuation to allow the machine to be cycled by the operator’s foot so the operator can support he workpiece in his/her hands
- PLC machine control with dual palm button actuation
- Dual opto-touch actuation upgrade (requires the selection of the bench-top base assembly) to allow for lower effort operator actuation
Mechanical Options:
- Probe type safety device to disable the machine if there are any obstructions in the rivet setting area
- Spare tooling package (Jaws / Drivers / Rollsets) to supplement the tooling that comes standard with the machine
- Bench-top base assembly (including controls package with footswitch and rollset holder) to allow for a complete bench-top rivet setting assembly machine
- Pedestal assembly (including controls package with footswitch and rollset holder) to allow for a complete floor standing rivet setting assembly machine
- Custom machine table designed and built to optimize the customer’s assembly process
- Quick Change raceway with one (1) set of tooling (Jaws / Driver / Rollset) to allow the riveting machine to be adapted to a different rivet size
- Vibratory hopper upgrade so the machine can hold additional rivets or if the rivets have a feature precluding the standard hopper bowl feeding method
- Load deflection device
- Part holding fixture to support the components prior to riveting
- Pilot operated check valve to allow for pressure relief
- Narrow Anvil Arm w/steel insert (customer part defined)

The Milford Model 255 is an electro-mechanical, flywheel driven, floor standing riveting machine; designed for operator loaded assembly applications. This single spindle riveter will automatically feed and set one semi-tubular rivet per cycle. Our standard unit comes equipped with a 120 volt motor, and controls for footswitch actuation. The cycle time of the riveter is under 1 second allowing for quick and efficient assembly operations. Typical applications where these units are used include HVAC assemblies, hinged assemblies, furniture components, appliance components, electrical devices, brake shoes, etc.
Max Rivet Diameter | .125" (3.25mm) |
Max Rivet Length | .562" (14.25mm) |
Stroke | 2.5" (63.5mm) |
Weight | 535 lbs (242.5 kg) |
Throat Depth | 12.0" (304.5mm) |
- Download .eprt
- Download .step
Orbitform’s modular Milford Model 255 impact riveter is manufactured and assembled at Orbitform’s factory in Jackson, Michigan, USA. The impact riveting machine is available with many standard features and the impact assembly machine can be customized with options to help monitor, control, and improve the assembly process. Orbitform’s application engineers listen and seek the appropriate answer for each specific assembly process being considered. Orbitform’s team can outline the required upper and lower tooling to conduct the riveting application and, if the customer desires, Orbitform can design and build turnkey assembly machines complete with machine actuation, safety system, fixturing method, error proofing process, and/or other expert assembly features associated with impact riveting machines and automatic assembly equipment.
The robust design of this riveting machine results in machines operating for 50 or more years in continual service. The Milford riveter's column, base, and frame offer the strength required for the most demanding semi-tubular riveting applications in the world.
Standard Impact Rivet Machine Features and Specifications
- 5.25” diameter rotary mechanical hopper to store rivets to be automatically released to the machine
- Machine actuation: Standard unit shipped with guarded footswitch
- Tooling: (1) set of engineered-to-suit tooling is included (Jaws / Driver / Rollset)
Impact Rivet Machine Options:
Electrical Options:
- Controls package with footswitch actuation to allow the machine to be cycled by the operator’s foot so the operator can support he workpiece in his/her hands
- PLC machine control with dual palm button actuation
- Dual opto-touch actuation upgrade (requires a part holding fixture) to allow for lower effort operator actuation
Mechanical Options:
- Probe type safety device to disable the machine if there are any obstructions in the rivet setting area
- Spare tooling package (Jaws / Drivers / Rollsets) to supplement the tooling that comes standard with the machine
- Quick Change raceway with one (1) set of tooling (Jaws / Driver / Rollset) to allow the riveting machine to be adapted to a different rivet size
- Vibratory hopper upgrade so the machine can hold additional rivets or if the rivets have a feature precluding the standard hopper bowl feeding method
- Part holding fixture to support the components prior to riveting
- Narrow Anvil Arm w/steel insert (customer part defined)
- Altered lower rollset holder (customer part defined)
- Tonnage Monitor to precisely determine the force being applied
- Continuous drive hopper to help keep rivets flowing through the hopper and reduce the possibility of rivets sticking

The Milford Model 256 is an electro-mechanical, flywheel driven, floor standing riveting machine; designed for operator loaded assembly applications. This single spindle riveter will automatically feed and set one semi-tubular rivet per cycle. Our standard unit comes equipped with a 120 volt motor, and controls for footswitch actuation. The cycle time of the riveter is under 1 second allowing for quick and efficient assembly operations. Typical applications where these units are used include HVAC assemblies, hinged assemblies, furniture components, appliance components, electrical devices, brake shoes, etc.
Max Rivet Diameter | .156" (3.25mm) |
Max Rivet Length | .75" (14.25mm) |
Stroke | 2.5" (63.5mm) |
Weight | 550 lbs (250 kg) |
Throat Depth | 12.0" (304.5mm) |
- Download .eprt
- Download .step
Orbitform’s Milford Model 256 impact riveter is manufactured and assembled at Orbitform’s factory in Jackson, Michigan, USA. The impact riveting machine is available with many standard features and the impact assembly machine can be customized with options to help monitor, control, and improve the assembly process. Orbitform’s application engineers listen and seek the appropriate answer for each specific assembly process being considered. Orbitform’s team can outline the required upper and lower tooling to conduct the riveting application and, if the customer desires, Orbitform can design and build turnkey assembly machines complete with machine actuation, safety system, fixturing method, error proofing process, and/or other expert assembly features associated with impact riveting machines and automatic assembly equipment.
The robust design of this riveting machine results in machines operating for 50 or more years in continual service. The Milford riveter's column, base, and frame offer the strength required for the most demanding semi-tubular riveting applications in the world.
Standard Impact Rivet Machine Features and Specifications
- 7.5” diameter rotary mechanical hopper to store rivets to be automatically released to the machine
- Machine actuation: Standard unit shipped with guarded footswitch
- Tooling: (1) set of engineered-to-suit tooling is included (Jaws / Driver / Rollset)
Impact Rivet Machine Options:
Electrical Options:
- Controls package with footswitch actuation to allow the machine to be cycled by the operator’s foot so the operator can support he workpiece in his/her hands
- PLC machine control with dual palm button actuation
- Dual opto-touch actuation upgrade (requires a part holding fixture) to allow for lower effort operator actuation
Mechanical Options:
- Probe type safety device to disable the machine if there are any obstructions in the rivet setting area
- Spare tooling package (Jaws / Drivers / Rollsets) to supplement the tooling that comes standard with the machine
- Quick Change raceway with one (1) set of tooling (Jaws / Driver / Rollset) to allow the riveting machine to be adapted to a different rivet size
- Vibratory hopper upgrade so the machine can hold additional rivets or if the rivets have a feature precluding the standard hopper bowl feeding method
- Part holding fixture to support the components prior to riveting
- Narrow Anvil Arm w/steel insert (customer part defined)
- Altered lower rollset holder (customer part defined)
- Tonnage Monitor to precisely determine the force being applied
- Continuous drive hopper to help keep rivets flowing through the hopper and reduce the possibility of rivets sticking

The Milford Model 305 is an electro-mechanical, flywheel driven, floor standing riveting machine; designed for operator loaded assembly applications. This single spindle riveter will automatically feed and set one semi-tubular rivet per cycle. Our standard unit comes equipped with a 120 volt motor, and controls for footswitch actuation. The cycle time of the riveter is under 1 second allowing for quick and efficient assembly operations. Typical applications where these units are used include HVAC assemblies, hinged assemblies, furniture components, appliance components, electrical devices, brake shoes, etc.
Max Rivet Diameter | .187" |
Max Rivet Length | .75" |
Stroke | 3.5" |
Weight | 690 lbs |
Throat Depth | 12.0" (304.5mm) |
- Download .eprt
- Download .step
Orbitform’s modular Milford Model 305 impact riveter is manufactured and assembled at Orbitform’s factory in Jackson, Michigan, USA. The impact riveting machine is available with many standard features and the impact assembly machine can be customized with options to help monitor, control, and improve the assembly process. Orbitform’s application engineers listen and seek the appropriate answer for each specific assembly process being considered. Orbitform’s team can outline the required upper and lower tooling to conduct the riveting application and, if the customer desires, Orbitform can design and build turnkey assembly machines complete with machine actuation, safety system, fixturing method, error proofing process, and/or other expert assembly features associated with impact riveting machines and automatic assembly equipment.
The robust design of this riveting machine results in machines operating for 50 or more years in continual service. The Milford riveter's column, base, and frame offer the strength required for the most demanding semi-tubular riveting applications in the world.
Standard Impact Rivet Machine Features and Specifications
- 7.5” diameter rotary mechanical hopper to store rivets to be automatically released to the machine
- Machine actuation: Standard unit shipped with guarded footswitch
- Tooling: (1) set of engineered-to-suit tooling is included (Jaws / Driver / Rollset)
Impact Rivet Machine Options:
Electrical Options:
- Controls package with footswitch actuation to allow the machine to be cycled by the operator’s foot so the operator can support he workpiece in his/her hands
- PLC machine control with dual palm button actuation
- Dual opto-touch actuation upgrade (requires a part holding fixture) to allow for lower effort operator actuation
Mechanical Options:
- Probe type safety device to disable the machine if there are any obstructions in the rivet setting area
- Spare tooling package (Jaws / Drivers / Rollsets) to supplement the tooling that comes standard with the machine
- Quick Change raceway with one (1) set of tooling (Jaws / Driver / Rollset) to allow the riveting machine to be adapted to a different rivet size
- Vibratory hopper upgrade so the machine can hold additional rivets or if the rivets have a feature precluding the standard hopper bowl feeding method
- Part holding fixture to support the components prior to riveting
- Narrow Anvil Arm w/steel insert (customer part defined)
- Altered lower rollset holder (customer part defined)
- Tonnage Monitor to precisely determine the force being applied
- Continuous drive hopper to help keep rivets flowing through the hopper and reduce the possibility of rivets sticking
- Available with a 24" (610mm) throat depth for applications where the part being assembled is large

The Milford Model 310 is an electro-mechanical, flywheel driven, floor standing riveting machine; designed for operator loaded assembly applications. This single spindle riveter will automatically feed and set one semi-tubular rivet per cycle. Our standard unit comes equipped with a 120 volt motor, and controls for footswitch actuation. The cycle time of the riveter is under 1 second allowing for quick and efficient assembly operations. Typical applications where these units are used include HVAC assemblies, hinged assemblies, furniture components, appliance components, electrical devices, brake shoes, etc.
Max Rivet Diameter | .187" (4.75mm) |
Max Rivet Length | 1.0" (25.5mm) |
Stroke | 3.5" (89mm) |
Weight | 715 lbs (324 kg) |
Throat Depth | 12.0" (304.5mm) |
- Download .eprt
- Download .step
Orbitform’s Milford Model 310 impact riveter is manufactured and assembled at Orbitform’s factory in Jackson, Michigan, USA. The impact riveting machine is available with many standard features and the impact assembly machine can be customized with options to help monitor, control, and improve the assembly process. Orbitform’s application engineers listen and seek the appropriate answer for each specific assembly process being considered. Orbitform’s team can outline the required upper and lower tooling to conduct the riveting application and, if the customer desires, Orbitform can design and build turnkey assembly machines complete with machine actuation, safety system, fixturing method, error proofing process, and/or other expert assembly features associated with impact riveting machines and automatic assembly equipment.
The robust design of this riveting machine results in machines operating for 50 or more years in continual service. The Milford riveter's column, base, and frame offer the strength required for the most demanding semi-tubular riveting applications in the world.
Standard Impact Rivet Machine Features and Specifications
- 7.5” diameter rotary mechanical hopper to store rivets to be automatically released to the machine
- Machine actuation: Standard unit shipped with guarded footswitch
- Tooling: (1) set of engineered-to-suit tooling is included (Jaws / Driver / Rollset)
Impact Rivet Machine Options:
Electrical Options:
- Controls package with footswitch actuation to allow the machine to be cycled by the operator’s foot so the operator can support he workpiece in his/her hands
- PLC machine control with dual palm button actuation
- Dual opto-touch actuation upgrade (requires a part holding fixture) to allow for lower effort operator actuation
Mechanical Options:
- Probe type safety device to disable the machine if there are any obstructions in the rivet setting area
- Spare tooling package (Jaws / Drivers / Rollsets) to supplement the tooling that comes standard with the machine
- Quick Change raceway with one (1) set of tooling (Jaws / Driver / Rollset) to allow the riveting machine to be adapted to a different rivet size
- Vibratory hopper upgrade so the machine can hold additional rivets or if the rivets have a feature precluding the standard hopper bowl feeding method
- Part holding fixture to support the components prior to riveting
- Narrow Anvil Arm w/steel insert (customer part defined)
- Altered lower rollset holder (customer part defined)
- Tonnage Monitor to precisely determine the force being applied
- Continuous drive hopper to help keep rivets flowing through the hopper and reduce the possibility of rivets sticking
- Available with a 24" (610mm) throat depth for applications where the part being assembled is large

The Milford Model 313 is an electro-mechanical, flywheel driven, floor standing riveting machine; designed for operator loaded assembly applications. This single spindle riveter will automatically feed and set one semi-tubular rivet per cycle. Our standard unit comes equipped with a 120 volt motor, and controls for footswitch actuation. The cycle time of the riveter is under 1 second allowing for quick and efficient assembly operations. The 313 is equipped with a continuous drive mechanical hopper to assist in the feeding of rivets up to 1.38” in length. Typical applications where these units are used include HVAC assemblies, hinged assemblies, furniture components, appliance components, electrical devices, brake shoes, etc.
Max Rivet Diameter | 0.187" (4.75mm) |
Max Rivet Length | 1.375" (35mm) |
Stroke | 3.5" (89mm) |
Weight | 755 lbs (343 kg) |
Throat Depth | 12.0" (304.5mm) |
- Download .eprt
- Download .step
Orbitform’s modular Milford Model 313 impact riveter is manufactured and assembled at Orbitform’s factory in Jackson, Michigan, USA. The impact riveting machine is available with many standard features and the impact assembly machine can be customized with options to help monitor, control, and improve the assembly process. Orbitform’s application engineers listen and seek the appropriate answer for each specific assembly process being considered. Orbitform’s team can outline the required upper and lower tooling to conduct the riveting application and, if the customer desires, Orbitform can design and build turnkey assembly machines complete with machine actuation, safety system, fixturing method, error proofing process, and/or other expert assembly features associated with impact riveting machines and automatic assembly equipment.
The robust design of this riveting machine results in machines operating for 50 or more years in continual service. The Milford riveter's column, base, and frame offer the strength required for the most demanding semi-tubular riveting applications in the world.
Standard Impact Rivet Machine Features and Specifications
- 7.5” diameter rotary mechanical hopper to store rivets to be automatically released to the machine
- Machine actuation: Standard unit shipped with guarded footswitch
- Tooling: (1) set of engineered-to-suit tooling is included (Jaws / Driver / Rollset)
Impact Rivet Machine Options:
Electrical Options:
- Controls package with footswitch actuation to allow the machine to be cycled by the operator’s foot so the operator can support he workpiece in his/her hands
- PLC machine control with dual palm button actuation
- Dual opto-touch actuation upgrade (requires a part holding fixture) to allow for lower effort operator actuation
Mechanical Options:
- Probe type safety device to disable the machine if there are any obstructions in the rivet setting area
- Spare tooling package (Jaws / Drivers / Rollsets) to supplement the tooling that comes standard with the machine
- Quick Change raceway with one (1) set of tooling (Jaws / Driver / Rollset) to allow the riveting machine to be adapted to a different rivet size
- Vibratory hopper upgrade so the machine can hold additional rivets or if the rivets have a feature precluding the standard hopper bowl feeding method
- Part holding fixture to support the components prior to riveting
- Narrow Anvil Arm w/steel insert (customer part defined)
- Altered lower rollset holder (customer part defined)
- Tonnage Monitor to precisely determine the force being applied
- Available with a 24" (610mm) throat depth for applications where the part being assembled is large

The Milford Model 405 is an electro-mechanical, flywheel driven, floor standing riveting machine; designed for operator loaded assembly applications. This single spindle riveter will automatically feed and set one semi-tubular rivet per cycle. Our standard unit comes equipped with a 120 volt motor, and controls for footswitch actuation. The cycle time of the riveter is under 1 second allowing for quick and efficient assembly operations. Able to form rivets up to 0.25" diameter, this model riveter is very useful and versatile. Typical applications where these units are used include HVAC assemblies, hinged assemblies, furniture components, appliance components, electrical devices, brake shoes, etc.
Max Rivet Diameter | .25" (6.5 mm) |
Max Rivet Length | .75" (19.0mm) |
Stroke | 3.5" (89mm) |
Weight | 755 lbs (343 kg) |
Throat Depth | 12.0" (304.5mm) |
- Download .eprt
- Download .step
Orbitform’s Milford Model 405 impact riveter is manufactured and assembled at Orbitform’s factory in Jackson, Michigan, USA. The impact riveting machine is available with many standard features and the impact assembly machine can be customized with options to help monitor, control, and improve the assembly process. Orbitform’s application engineers listen and seek the appropriate answer for each specific assembly process being considered. Orbitform’s team can outline the required upper and lower tooling to conduct the riveting application and, if the customer desires, Orbitform can design and build turnkey assembly machines complete with machine actuation, safety system, fixturing method, error proofing process, and/or other expert assembly features associated with impact riveting machines and automatic assembly equipment.
The robust design of this riveting machine results in machines operating for 50 or more years in continual service. The Milford riveter's column, base, and frame offer the strength required for the most demanding semi-tubular riveting applications in the world.
Standard Impact Rivet Machine Features and Specifications
- 7.5” diameter rotary mechanical hopper to store rivets to be automatically released to the machine
- Machine actuation: Standard unit shipped with guarded footswitch
- Tooling: (1) set of engineered-to-suit tooling is included (Jaws / Driver / Rollset)
Impact Rivet Machine Options:
Electrical Options:
- Controls package with footswitch actuation to allow the machine to be cycled by the operator’s foot so the operator can support he workpiece in his/her hands
- PLC machine control with dual palm button actuation
- Dual opto-touch actuation upgrade (requires a part holding fixture) to allow for lower effort operator actuation
Mechanical Options:
- Probe type safety device to disable the machine if there are any obstructions in the rivet setting area
- Spare tooling package (Jaws / Drivers / Rollsets) to supplement the tooling that comes standard with the machine
- Quick Change raceway with one (1) set of tooling (Jaws / Driver / Rollset) to allow the riveting machine to be adapted to a different rivet size
- Vibratory hopper upgrade so the machine can hold additional rivets or if the rivets have a feature precluding the standard hopper bowl feeding method
- Part holding fixture to support the components prior to riveting
- Narrow Anvil Arm w/steel insert (customer part defined)
- Altered lower rollset holder (customer part defined)
- Tonnage Monitor to precisely determine the force being applied
- Continuous drive hopper to help keep rivets flowing through the hopper and reduce the possibility of rivets sticking
- Available with a 24" (610mm) throat depth for applications where the part being assembled is large

The Milford Model 410 is an electro-mechanical, flywheel driven, floor standing riveting machine; designed for operator loaded assembly applications. This single spindle riveter will automatically feed and set one semi-tubular rivet per cycle. Our standard unit comes equipped with a 120 volt motor, and controls for footswitch actuation. The cycle time of the riveter is under 1 second allowing for quick and efficient assembly operations. Able to form rivets up to 0.25" diameter, this model riveter is very useful and versatile. Typical applications where these units are used include HVAC assemblies, hinged assemblies, furniture components, appliance components, electrical devices, brake shoes, etc.
Max Rivet Diameter | .25" (6.5 mm) |
Max Rivet Length | 1.0" (25.5mm) |
Stroke | 3.5" (89mm) |
Weight | 870 lbs (395 kg) |
Throat Depth | 12.0" (304.5mm) |
- Download .eprt
- Download .step
Orbitform’s Milford Model 410 impact riveter is manufactured and assembled at Orbitform’s factory in Jackson, Michigan, USA. The impact riveting machine is available with many standard features and the impact assembly machine can be customized with options to help monitor, control, and improve the assembly process. Orbitform’s application engineers listen and seek the appropriate answer for each specific assembly process being considered. Orbitform’s team can outline the required upper and lower tooling to conduct the riveting application and, if the customer desires, Orbitform can design and build turnkey assembly machines complete with machine actuation, safety system, fixturing method, error proofing process, and/or other expert assembly features associated with impact riveting machines and automatic assembly equipment.
The robust design of this riveting machine results in machines operating for 50 or more years in continual service. The Milford riveter's column, base, and frame offer the strength required for the most demanding semi-tubular riveting applications in the world.
Standard Impact Rivet Machine Features and Specifications
- 7.5” diameter rotary mechanical hopper to store rivets to be automatically released to the machine
- Machine actuation: Standard unit shipped with guarded footswitch
- Tooling: (1) set of engineered-to-suit tooling is included (Jaws / Driver / Rollset)
Impact Rivet Machine Options:
Electrical Options:
- Controls package with footswitch actuation to allow the machine to be cycled by the operator’s foot so the operator can support he workpiece in his/her hands
- PLC machine control with dual palm button actuation
- Dual opto-touch actuation upgrade (requires a part holding fixture) to allow for lower effort operator actuation
Mechanical Options:
- Probe type safety device to disable the machine if there are any obstructions in the rivet setting area
- Spare tooling package (Jaws / Drivers / Rollsets) to supplement the tooling that comes standard with the machine
- Quick Change raceway with one (1) set of tooling (Jaws / Driver / Rollset) to allow the riveting machine to be adapted to a different rivet size
- Vibratory hopper upgrade so the machine can hold additional rivets or if the rivets have a feature precluding the standard hopper bowl feeding method
- Part holding fixture to support the components prior to riveting
- Narrow Anvil Arm w/steel insert (customer part defined)
- Altered lower rollset holder (customer part defined)
- Tonnage Monitor to precisely determine the force being applied
- Continuous drive hopper to help keep rivets flowing through the hopper and reduce the possibility of rivets sticking
- Available with a 24" (610mm) throat depth for applications where the part being assembled is large

The Milford Model 413 is an electro-mechanical, flywheel driven, floor standing riveting machine; designed for operator loaded assembly applications. This single spindle riveter will automatically feed and set one semi-tubular rivet per cycle. Our standard unit comes equipped with a 120 volt motor, and controls for footswitch actuation. The cycle time of the riveter is under 1 second allowing for quick and efficient assembly operations. The 413 is equipped with a continuous drive mechanical hopper to assist in the feeding of rivets up to 1.38” in length. Typical applications where these units are used include HVAC assemblies, hinged assemblies, furniture components, appliance components, electrical devices, brake shoes, etc.
Max Rivet Diameter | .25" (6.5 mm) |
Max Rivet Length | 1.375" (35mm) |
Stroke | 3.5" (89mm) |
Weight | 900 lbs (409 kg) |
Throat Depth | 12.0" (304.5mm) |
- Download .eprt
- Download .step
Orbitform’s Milford Model 413 impact riveter is manufactured and assembled at Orbitform’s factory in Jackson, Michigan, USA. The impact riveting machine is available with many standard features and the impact assembly machine can be customized with options to help monitor, control, and improve the assembly process. Orbitform’s application engineers listen and seek the appropriate answer for each specific assembly process being considered. Orbitform’s team can outline the required upper and lower tooling to conduct the riveting application and, if the customer desires, Orbitform can design and build turnkey assembly machines complete with machine actuation, safety system, fixturing method, error proofing process, and/or other expert assembly features associated with impact riveting machines and automatic assembly equipment.
The robust design of this riveting machine results in machines operating for 50 or more years in continual service. The Milford riveter's column, base, and frame offer the strength required for the most demanding semi-tubular riveting applications in the world.
Standard Impact Rivet Machine Features and Specifications
- 7.5” diameter rotary mechanical hopper to store rivets to be automatically released to the machine
- Machine actuation: Standard unit shipped with guarded footswitch
- Tooling: (1) set of engineered-to-suit tooling is included (Jaws / Driver / Rollset)
Impact Rivet Machine Options:
Electrical Options:
- Controls package with footswitch actuation to allow the machine to be cycled by the operator’s foot so the operator can support he workpiece in his/her hands
- PLC machine control with dual palm button actuation
- Dual opto-touch actuation upgrade (requires a part holding fixture) to allow for lower effort operator actuation
Mechanical Options:
- Probe type safety device to disable the machine if there are any obstructions in the rivet setting area
- Spare tooling package (Jaws / Drivers / Rollsets) to supplement the tooling that comes standard with the machine
- Quick Change raceway with one (1) set of tooling (Jaws / Driver / Rollset) to allow the riveting machine to be adapted to a different rivet size
- Vibratory hopper upgrade so the machine can hold additional rivets or if the rivets have a feature precluding the standard hopper bowl feeding method
- Part holding fixture to support the components prior to riveting
- Narrow Anvil Arm w/steel insert (customer part defined)
- Altered lower rollset holder (customer part defined)
- Tonnage Monitor to precisely determine the force being applied
- Available with a 24" (610mm) throat depth for applications where the part being assembled is large

The Milford Model 423 is an electro-mechanical, flywheel driven, floor standing riveting machine; designed for operator loaded assembly applications. This single spindle riveter will automatically feed and set one semi-tubular rivet per cycle. Our standard unit comes equipped with a 120 volt motor, and controls for footswitch actuation. The cycle time of the riveter is under 1 second allowing for quick and efficient assembly operations. The 423 is equipped with a vibratory hopper to assist in the feeding of rivets up to 3” in length. The vibratory hopper is also recommended when feeding and inserting special fasteners. Typical applications where these units are used include HVAC assemblies, hinged assemblies, furniture components, appliance components, electrical devices, brake shoes, etc.
Max Rivet Diameter | .25" (6.5 mm) |
Max Rivet Length | 3.0" (76.25mm) |
Stroke | 5.5" (140mm) |
Weight | 900 lbs (409 kg) |
Throat Depth | 12.0" (304.5mm) |
- Download .dwg
- Download .easm
- Download .step
Orbitform’s Milford Model 423 impact riveter is manufactured and assembled at Orbitform’s factory in Jackson, Michigan, USA. The impact riveting machine is available with many standard features and the impact assembly machine can be customized with options to help monitor, control, and improve the assembly process. Orbitform’s application engineers listen and seek the appropriate answer for each specific assembly process being considered. Orbitform’s team can outline the required upper and lower tooling to conduct the riveting application and, if the customer desires, Orbitform can design and build turnkey assembly machines complete with machine actuation, safety system, fixturing method, error proofing process, and/or other expert assembly features associated with impact riveting machines and automatic assembly equipment.
The robust design of this riveting machine results in machines operating for 50 or more years in continual service. The Milford riveter's column, base, and frame offer the strength required for the most demanding semi-tubular riveting applications in the world.
Standard Impact Rivet Machine Features and Specifications
- Vibratory hopper to store rivets to be automatically released to the machine
- Machine actuation: Standard unit shipped with guarded footswitch
- Tooling: (1) set of engineered-to-suit tooling is included (Jaws / Driver / Rollset)
Impact Rivet Machine Options:
Electrical Options:
- Controls package with footswitch actuation to allow the machine to be cycled by the operator’s foot so the operator can support he workpiece in his/her hands
- PLC machine control with dual palm button actuation
- Dual opto-touch actuation upgrade (requires a part holding fixture) to allow for lower effort operator actuation
Mechanical Options:
- Probe type safety device to disable the machine if there are any obstructions in the rivet setting area
- Spare tooling package (Jaws / Drivers / Rollsets) to supplement the tooling that comes standard with the machine
- Quick Change raceway with one (1) set of tooling (Jaws / Driver / Rollset) to allow the riveting machine to be adapted to a different rivet size
- Part holding fixture to support the components prior to riveting
- Narrow Anvil Arm w/steel insert (customer part defined)
- Altered lower rollset holder (customer part defined)
- Tonnage Monitor to precisely determine the force being applied
- Available with a 24" (610mm) throat depth for applications where the part being assembled is large