摆碾铆机
Orbitform’s standard modular bench and pedestal machines offer a range of complete turn-key assembly solution for orbital riveting and forming for work pieces 0.125” dia. to over 1 inch (3.1 mm to 25 mm) for a consistent form.
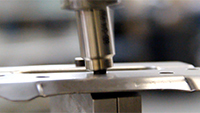
- 型号
- B-125
- B-240
- B-310
- B-500
- B-750
- B-840

Orbitform’s B-125 bench machine is designed for small work piece orbital riveting and radial riveting. The bench machine, comprised of an orbital forming modular powerhead, orbital head with developed peen, adjustable column, base with t-slots for easy fixture mounting, and complete controls, is commonly used to assemble electrical components, medical devices, computer hardware, small hand tools and other small scale riveted assemblies. Orbitform’s application engineers outline the required orbital head and orbital peen to conduct the riveting application and, if the customer desires, Orbitform can design and build custom machine actuation, a safety system, a fixturing method, an error proofing process, and/or other expert assembly features associated with orbital riveting machines and automatic assembly equipment.
Weight | 150 lbs |
Throat Depth | 3.5" (89 mm) |
Head Forming Capacity | .125" (3.25mm) |
Max Downward Force | 590 lbs @ 100 psi |
Max Stroke | 1.5" (38 mm) |
- Download .dwg
- Download .easm
- Download .step
Orbitform’s modular B-125 bench machine is manufactured and assembled at Orbitform’s factory in Jackson, Michigan, USA. The orbital riveting bench machine is available with many standard features and the orbital forming bench machine can be customized with options to help monitor, control, and improve the assembly process. Orbitform’s application engineers listen and seek the appropriate answer for each specific assembly process being considered. Orbitform can design and build a complete turnkey assembly system including controls, safety, fixtures, errorproofing, and more.
Standard Features and Specifications for Orbital Riveting or Orbital Forming Applications:
- Powerhead with electric motor and orbital head with peen developed and tested for each application
- Column and base assembly with 5" (127 mm) vertical powerhead height adjustment and t-slot base. These features allow for flexibility in machine setup and fixturing. A standard bench machine can easily be configured to an assortment of different assembly applications.
- HMI touch panel for enhanced diagnostics
- Directional valve with dual pilot operated (PO) check to prevent powerhead drifting
- Dual low actuation force palm buttons for cycling the machine
- Pneumatic solenoid valves to assist with smooth and exact fluid motion
- Filter-regulator unit with gauge to keep the air supply clean and protect the machine’s components
- Digital adjustable dwell timer
- Resettable cycle counter to keep track of machine cycles
- Electrical enclosure with disconnect switch
- Illuminated power on selector switch
- Programmable Logic Controller
Bench Machine Options:
Electrical Options
- Light curtains for operator safety
- PLC expansion for an additional I/O
- Low-profile LED worklight to enhance the lighting of the work area
- Home limit switch to acknowledge when the tool is fully retracted
Mechanical Options
- Precision machine base 24"W x 24"L x 30"H (610 mm W x 610 mm L x 760 mm H)
- Precision machine base with casters
- Guarding for operator safety
- Air line lubricator
- Custom part fixturing designed and built by Orbitform allowing a turnkey riveting solution
- Pneumatic fixture slide to allow for simpler part loading
- Offset motor mount to allow for a shorter machine height and/or to allow for a through spindle pressure pad
- Gear reducer to reduce the RPM to allow for the optimal forming speed
- Spindle brake to control the tool position or to stop the tool rotation for certain applications
- Anti-rotate device to prevent the peen from rotating during certain assembly or forming applications
- Orbital alignment kit to help you set up the machine if the machine configurations change
Error Proofing, Process Monitoring, Process Control Options
- Process Intelligence Package: Load Cell, LVDT (Linear Variable Displacement Transducer), Touch Screen
- Pressure pad (standard, height sensing, or programmable height sensing) to secure the work piece prior to forming or assembly, to assist with assembly process monitoring / process control, or to confirm part presence prior to continuing the assembly process
Forming Options
- Radial head for radial riveting or radial forming assembly applications when the radial forming process is preferred
- Static rollerhead for roller forming or roller assembly applications
- Press head powerhead configuration and press tooling to allow the powerhead to act as a press for pressing parts together into any assembly

Orbitform’s B-240 bench machine is designed for small to medium size work piece orbital riveting and radial riveting. The bench machine, comprised of an orbital forming modular powerhead, orbital head with developed peen, adjustable column, base with t-slots for easy fixture mounting, and complete controls, is commonly used to assemble electrical contacts, valves, cookware, small hinged products, sporting goods, and other small to medium scale riveted assemblies. Orbitform’s application engineers outline the required orbital head and orbital peen to conduct the riveting application and, if the customer desires, Orbitform can design and build custom machine actuation, a safety system, a fixturing method, an error proofing process, and/or other expert assembly features associated with orbital riveting machines and automatic assembly equipment.
Weight | 250 lbs |
Throat Depth | 4.5" (114mm) |
Head Forming Capacity | .236" (6mm) |
Max Downward Force | 1460 lbs @ 100 psi |
Max Stroke | 1.75" (44.5mm) |
- Download .dwg
- Download .easm
- Download .step
Orbitform’s modular B-240 bench machine is manufactured and assembled at Orbitform’s factory in Jackson, Michigan, USA. The orbital riveting bench machine is available with many standard features and the orbital forming bench machine can be customized with options to help monitor, control, and improve the assembly process. Orbitform’s application engineers listen and seek the appropriate answer for each specific assembly process being considered. Orbitform can design and build a complete turnkey assembly system including controls, safety, fixtures, error-proofing, and more.
Standard Features and Specifications for Orbital Riveting or Orbital Forming Applications:
- Powerhead with electric motor and orbital head with peen developed and tested for each application
- Column and base assembly with 5" (127 mm) vertical powerhead height adjustment and t-slot base. These features allow for flexibility in machine setup and fixturing. A standard bench machine can easily be configured to an assortment of different assembly applications.
- HMI touch panel for enhanced diagnostics
- Directional valve with dual pilot operated (PO) check to prevent powerhead drifting
- Dual low actuation force palm buttons for cycling the machine
- Pneumatic solenoid valves to assist with smooth and exact fluid motion
- Filter-regulator unit with gauge to keep the air supply clean and protect the machine’s components
- Digital adjustable dwell timer
- Resettable cycle counter to keep track of machine cycles
- Electrical enclosure with disconnect switch
- Illuminated power on selector switch
- Programmable Logic Controller
Bench Machine Options:
Electrical Options
- Light curtains for operator safety
- PLC expansion for an additional I/O
- Low-profile LED work light to enhance the lighting of the work area
- Home limit switch to acknowledge when the tool is fully retracted
Mechanical Options
- Precision machine base 24"W x 24"L x 30"H (610 mm W x 610 mm L x 760 mm H)
- Precision machine base with casters
- Guarding for operator safety
- Air line lubricator
- Custom part fixturing designed and built by Orbitform allowing a turnkey riveting solution
- Pneumatic fixture slide to allow for simpler part loading
- Offset motor mount to allow for a shorter machine height and/or to allow for a through spindle pressure pad
- Gear reducer to reduce the RPM to allow for the optimal forming speed
- Spindle brake to control the tool position or to stop the tool rotation for certain applications
- Anti-rotate device to prevent the peen from rotating during certain assembly or forming applications
- Orbital alignment kit to help you set up the machine if the machine configurations change
Error Proofing, Process Monitoring, Process Control Options
- Process Intelligence Package: Load Cell, LVDT (Linear Variable Displacement Transducer), Touch Screen
- Pressure pad (standard, height sensing, or programmable height sensing) to secure the work piece prior to forming or assembly, to assist with assembly process monitoring / process control, or to confirm part presence prior to continuing the assembly process
Forming Options
- Radial head for radial riveting or radial forming assembly applications when the radial forming process is preferred
- Multi-point or Multi-spindle head for orbital riveting or orbital forming of multiple rivets at the same time
- Static rollerhead for roller forming or roller assembly applications
- Articulating rollerhead for roller forming or roller assembly applications
- Press head powerhead configuration and press tooling to allow the powerhead to act as a press for pressing parts together into any assembly

Orbitform’s B-310 bench machine is designed for medium size work piece orbital riveting and radial riveting. The bench machine, comprised of an orbital forming modular powerhead, orbital head with developed peen, adjustable column, base with t-slots for easy fixture mounting, and complete controls, is commonly used with assembly machines for HVAC products, hinged assemblies, brake pads, turbine and hub assemblies, clamps, and other medium scale riveted assemblies. Orbitform’s application engineers outline the required orbital head and orbital peen to conduct the riveting application and, if the customer desires, Orbitform can design and build custom machine actuation, a safety system, a fixturing method, an error proofing process, and/or other expert assembly features associated with orbital riveting machines and automatic assembly equipment.
Servo powerhead option available.
Weight | 580 lbs |
Throat Depth | 6.25" (158.75mm) |
Head Forming Capacity | .312" (8mm) |
Max Downward Force | 2120 lbs @ 100 psi |
Max Stroke | 2.0" (51mm) |
- Download .dwg
- Download .easm
- Download .step
Orbitform’s modular B-310 bench machine is manufactured and assembled at Orbitform’s factory in Jackson, Michigan, USA. The orbital riveting bench machine is available with many standard features and the orbital forming bench machine can be customized with options to help monitor, control, and improve the assembly process. Orbitform’s application engineers listen and seek the appropriate answer for each specific assembly process being considered. Orbitform can design and build a complete turnkey assembly system including controls, safety, fixtures, error proofing, and more.
Extended stroke requirements?
Applications with similar orbital riveting or orbital forming force but requiring extended vertical clearance for part loading may benefit from the extended stroke Orbitform powerhead model B-320.
- The B-320 Orbitform powerhead has a total tool stroke distance of 2.5 in (64 mm) that is adjustable between 0 in to 2.5 in (0 mm to 64 mm).
Standard Features and Specifications for Orbital Riveting or Orbital Forming Applications:
- Powerhead with electric motor and orbital head with peen developed and tested for each application
- Column and base assembly with 5" (127 mm) vertical powerhead height adjustment and t-slot base. These features allow for flexibility in machine setup and fixturing. A standard bench machine can easily be configured to an assortment of different assembly applications.
- HMI touch panel for enhanced diagnostics
- Directional valve with dual pilot operated (PO) check to prevent powerhead drifting
- Dual low actuation force palm buttons for cycling the machine
- Pneumatic solenoid valves to assist with smooth and exact fluid motion
- Filter-regulator unit with gauge to keep the air supply clean and protect the machine’s components
- Digital adjustable dwell timer
- Resettable cycle counter to keep track of machine cycles
- Electrical enclosure with disconnect switch
- Illuminated power on selector switch
- Programmable Logic Controller
Bench Machine Options:
Electrical Options
- Light curtains for operator safety
- PLC expansion for an additional I/O
- Low-profile LED worklight to enhance the lighting of the work area
- Home limit switch to acknowledge when the tool is fully retracted
Mechanical Options
- Precision machine base 24"W x 24"L x 30"H (610 mm W x 610 mm L x 760 mm H)
- Precision machine base with casters
- Guarding for operator safety
- Air line lubricator
- Custom part fixturing designed and built by Orbitform allowing a turnkey riveting solution
- Pneumatic fixture slide to allow for simpler part loading
- Offset motor mount to allow for a shorter machine height and/or to allow for a through spindle pressure pad
- Gear reducer to reduce the RPM to allow for the optimal forming speed
- Spindle brake to control the tool position or to stop the tool rotation for certain applications
- Anti-rotate device to prevent the peen from rotating during certain assembly or forming applications
- Orbital alignment kit to help you set up the machine if the machine configurations change
Error Proofing, Process Monitoring, Process Control Options
- Process Intelligence Package: Load Cell, LVDT (Linear Variable Displacement Transducer), Touch Screen
- Pressure pad (standard, height sensing, or programmable height sensing) to secure the work piece prior to forming or assembly, to assist with assembly process monitoring / process control, or to confirm part presence prior to continuing the assembly process
Forming Options
- Radial head for radial riveting or radial forming assembly applications when the radial forming process is preferred
- Multi-point or Multi-spindle head for orbital riveting or orbital forming of multiple rivets at the same time
- Static rollerhead for roller forming or roller assembly applications
- Articulating rollerhead for roller forming or roller assembly applications
- Press head powerhead configuration and press tooling to allow the powerhead to act as a press for pressing parts together into any assembly

Orbitform’s B-500 bench machine is designed for medium to large size work piece orbital riveting, radial riveting, and tumble riveting. The bench machine, comprised of an orbital forming modular powerhead, orbital head with developed peen, adjustable column, base with t-slots for easy fixture mounting, and complete controls, is commonly used with riveting machines that assemble door and hood hinges, seat track structures, striker assemblies, furniture sub-assemblies, various automotive components, and other medium to large scale riveted assemblies. Orbitform’s application engineers outline the required orbital head and orbital peen to conduct the riveting application and, if the customer desires, Orbitform can design and build custom machine actuation, a safety system, a fixturing method, an error proofing process, and/or other expert assembly features associated with orbital riveting machines and automatic assembly equipment.
Servo powerhead option available.
Weight | 1000 lbs |
Throat Depth | 9.25" (234mm) |
Head Forming Capacity | .500" (12.75mm) |
Max Downward Force | 4400 lbs @ 100 psi |
Max Stroke | 2.5" (63.5mm) |
- Download .dwg
- Download .easm
- Download .step
Orbitform’s modular B-500 bench machine is manufactured and assembled at Orbitform’s factory in Jackson, Michigan, USA. The orbital riveting (tumble riveting) bench machine is available with many standard features and the orbital forming bench machine can be customized with options to help monitor, control, and improve the assembly process. Orbitform’s application engineers listen and seek the appropriate answer for each specific assembly process being considered. Orbitform can design and build a complete turnkey assembly system including controls, safety, fixtures, errorproofing, and more.
Extended stroke requirements?
Applications with similar orbital riveting or orbital forming force but requiring extended vertical clearance for part loading may benefit from the extended stroke Orbitform bench machine models B-503 or B-506.
- The B-503 Orbitform bench machine has a total tool stroke distance of 3.25 in (82 mm) that is adjustable between 1.6 in to 3.25 in (41 mm to 82 mm).
- The B-506 Orbitform bench machine has a total tool stroke distance of 6 in (152 mm) that is adjustable between 3 in to 6 in (76 mm to 152 mm).
Standard Features and Specifications for Orbital Riveting or Orbital Forming Applications:
- Powerhead with electric motor and orbital head with peen developed and tested for each application
- Column and base assembly with 5" (127 mm) vertical powerhead height adjustment and t-slot base. These features allow for flexibility in machine setup and fixturing. A standard bench machine can easily be configured to an assortment of different assembly applications.
- HMI touch panel for enhanced diagnostics
- Directional valve with dual pilot operated (PO) check to prevent powerhead drifting
- Dual low actuation force palm buttons for cycling the machine
- Pneumatic solenoid valves to assist with smooth and exact fluid motion
- Filter-regulator unit with gauge to keep the air supply clean and protect the machine’s components
- Digital adjustable dwell timer
- Resettable cycle counter to keep track of machine cycles
- Electrical enclosure with disconnect switch
- Illuminated power on selector switch
- Programmable Logic Controller
Bench Machine Options:
Electrical Options
- Light curtains for operator safety
- PLC expansion for an additional I/O
- Low-profile LED worklight to enhance the lighting of the work area
- Home limit switch to acknowledge when the tool is fully retracted
Mechanical Options
- Precision machine base 24"W x 24"L x 30"H (610 mm W x 610 mm L x 760 mm H)
- Precision machine base with casters
- Guarding for operator safety
- Air line lubricator
- Custom part fixturing designed and built by Orbitform allowing a turnkey riveting solution
- Pneumatic fixture slide to allow for simpler part loading
- Offset motor mount to allow for a shorter machine height and/or to allow for a through spindle pressure pad
- Gear reducer to reduce the RPM to allow for the optimal forming speed
- Spindle brake to control the tool position or to stop the tool rotation for certain applications
- Anti-rotate device to prevent the peen from rotating during certain assembly or forming applications
- Orbital alignment kit to help you set up the machine if the machine configurations change
Error Proofing, Process Monitoring, Process Control Options
- Process Intelligence Package: Load Cell, LVDT (Linear Variable Displacement Transducer), Touch Screen
- Pressure pad (standard, height sensing, or programmable height sensing) to secure the work piece prior to forming or assembly, to assist with assembly process monitoring / process control, or to confirm part presence prior to continuing the assembly process
Forming Options
- Radial head for radial riveting or radial forming assembly applications when the radial forming process is preferred
- Multi-point or Multi-spindle head for orbital riveting, tumble riveting or orbital forming of multiple rivets at the same time
- Static rollerhead for roller forming or roller assembly applications
- Articulating rollerhead for roller forming or roller assembly applications
- Press head powerhead configuration and press tooling to allow the powerhead to act as a press for pressing parts together into any assembly

Orbitform’s B-750 bench machine is designed for medium to large size work piece orbital riveting, radial riveting, and wobble riveting. The bench machine, comprised of an orbital forming modular powerhead, orbital head with developed peen, adjustable column, base with t-slots for easy fixture mounting, and complete controls, is commonly used to assemble robust hinges, large brackets, brake components, industrial hand tools, automotive foot pedals, ball stud assemblies, and other medium to large scale riveted assemblies. Orbitform’s application engineers outline the required orbital head and orbital peen to conduct the riveting application and, if the customer desires, Orbitform can design and build custom machine actuation, a safety system, a fixturing method, an error proofing process, and/or other expert assembly features associated with orbital riveting machines and automatic assembly equipment.
Servo powerhead option available.
Weight | 1100 lbs |
Throat Depth | 9.0" (228.5mm) |
Head Forming Capacity | .750" (19mm) |
Max Downward Force | 7510 lbs @ 100 psi |
Max Stroke | 2.5" (63.5mm) |
- Download .dwg
- Download .easm
- Download .step
Orbitform’s modular B-750 bench machine is manufactured and assembled at Orbitform’s factory in Jackson, Michigan, USA. The orbital riveting bench machine is available with many standard features and the orbital forming bench machine can be customized with options to help monitor, control, and improve the assembly process. Orbitform’s application engineers listen and seek the appropriate answer for each specific assembly process being considered. Orbitform can design and build a complete turnkey assembly system including controls, safety, fixtures, errorproofing, and more.
Extended stroke requirements?
Applications with similar orbital riveting or orbital forming force but requiring extended vertical clearance for part loading may benefit from the extended stroke Orbitform powerhead model B-753.
- The B-753 Orbitform powerhead has a total tool stroke distance of 3.0 in (76 mm) that is adjustable between 0 in to 3.0 in (0 mm to 76 mm).
Standard Features and Specifications for Orbital Riveting or Orbital Forming Applications:
- Powerhead with electric motor and orbital head with peen developed and tested for each application
- Column and base assembly with 5" (127 mm) vertical powerhead height adjustment and t-slot base. These features allow for flexibility in machine setup and fixturing. A standard bench machine can easily be configured to an assortment of different assembly applications.
- HMI touch panel for enhanced diagnostics
- Directional valve with dual pilot operated (PO) check to prevent powerhead drifting
- Dual low actuation force palm buttons for cycling the machine
- Pneumatic solenoid valves to assist with smooth and exact fluid motion
- Filter-regulator unit with gauge to keep the air supply clean and protect the machine’s components
- Digital adjustable dwell timer
- Resettable cycle counter to keep track of machine cycles
- Electrical enclosure with disconnect switch
- Illuminated power on selector switch
- Programmable Logic Controller
Bench Machine Options:
Electrical Options
- Light curtains for operator safety
- PLC expansion for an additional I/O
- Low-profile LED worklight to enhance the lighting of the work area
- Home limit switch to acknowledge when the tool is fully retracted
Mechanical Options
- Precision machine base 24"W x 24"L x 30"H (610 mm W x 610 mm L x 760 mm H)
- Precision machine base with casters
- Guarding for operator safety
- Air line lubricator
- Custom part fixturing designed and built by Orbitform allowing a turnkey riveting solution
- Pneumatic fixture slide to allow for simpler part loading
- Offset motor mount to allow for a shorter machine height and/or to allow for a through spindle pressure pad
- Gear reducer to reduce the RPM to allow for the optimal forming speed
- Spindle brake to control the tool position or to stop the tool rotation for certain applications
- Anti-rotate device to prevent the peen from rotating during certain assembly or forming applications
- Orbital alignment kit to help you set up the machine if the machine configurations change
Error Proofing, Process Monitoring, Process Control Options
- Process Intelligence Package: Load Cell, LVDT (Linear Variable Displacement Transducer), Touch Screen
- Pressure pad (standard, height sensing, or programmable height sensing) to secure the work piece prior to forming or assembly, to assist with assembly process monitoring / process control, or to confirm part presence prior to continuing the assembly process
Forming Options
- Radial head for radial riveting or radial forming assembly applications when the radial forming process is preferred
- Multi-point or Multi-spindle head for orbital riveting, orbital forming, or wobble riveting of multiple rivets at the same time
- Static rollerhead for roller forming or roller assembly applications
- Articulating rollerhead for roller forming or roller assembly applications
- Press head powerhead configuration and press tooling to allow the powerhead to act as a press for pressing parts together into any assembly

Orbitform’s B-840 bench machine is the highest capacity pneumatic orbital forming and orbital riveting bench machine available in the world. The Orbitform bench machine is perfectly suited for large size work piece orbital riveting processes and orbital cold forming assembly processes. The bench machine, comprised of an orbital forming modular powerhead, orbital head with developed peen, adjustable column, base with t-slots for easy fixture mounting, and complete controls, is commonly used to form spindle shafts, and assemble large automotive hinges, robust brake components, seat track products, and other large scale riveted assemblies. Orbitform’s application engineers outline the required orbital head and orbital peen to conduct the riveting application and, if the customer desires, Orbitform can design and build custom machine actuation, a safety system, a fixturing method, an error proofing process, and/or other expert assembly features associated with orbital riveting machines and automatic assembly equipment.
Weight | 1200 lbs |
Throat Depth | 9.0" (228.5mm) |
Head Forming Capacity | .840" (21.25mm) |
Max Downward Force | 12,700 lbs @ 100 psi |
Max Stroke | 2.5" (63.5mm) |
- Download .dwg
- Download .easm
- Download .step
Orbitform’s modular B-840 bench machine is manufactured and assembled at Orbitform’s factory in Jackson, Michigan, USA. The orbital riveting bench machine is available with many standard features and the orbital forming bench machine can be customized with options to help monitor, control, and improve the assembly process. Orbitform’s application engineers listen and seek the appropriate answer for each specific assembly process being considered. Orbitform can design and build a complete turnkey assembly system including controls, safety, fixtures, errorproofing, and more.
Standard Features and Specifications for Orbital Riveting or Orbital Forming Applications:
- Powerhead with electric motor and orbital head with peen developed and tested for each application
- Column and base assembly with 5" (127 mm) vertical powerhead height adjustment and t-slot base. These features allow for flexibility in machine setup and fixturing. A standard bench machine can easily be configured to an assortment of different assembly applications.
- HMI touch panel for enhanced diagnostics
- Directional valve with dual pilot operated (PO) check to prevent powerhead drifting
- Dual low actuation force palm buttons for cycling the machine
- Pneumatic solenoid valves to assist with smooth and exact fluid motion
- Filter-regulator unit with gauge to keep the air supply clean and protect the machine’s components
- Digital adjustable dwell timer
- Resettable cycle counter to keep track of machine cycles
- Electrical enclosure with disconnect switch
- Illuminated power on selector switch
- Programmable Logic Controller
Bench Machine Options:
Electrical Options
- Light curtains for operator safety
- PLC expansion for an additional I/O
- Low-profile LED worklight to enhance the lighting of the work area
- Home limit switch to acknowledge when the tool is fully retracted
Mechanical Options
- Precision machine base 24"W x 24"L x 30"H (610 mm W x 610 mm L x 760 mm H)
- Precision machine base with casters
- Guarding for operator safety
- Air line lubricator
- Custom part fixturing designed and built by Orbitform allowing a turnkey riveting solution
- Pneumatic fixture slide to allow for simpler part loading
- Offset motor mount to allow for a shorter machine height and/or to allow for a through spindle pressure pad
- Gear reducer to reduce the RPM to allow for the optimal forming speed
- Spindle brake to control the tool position or to stop the tool rotation for certain applications
- Anti-rotate device to prevent the peen from rotating during certain assembly or forming applications
- Orbital alignment kit to help you set up the machine if the machine configurations change
Error Proofing, Process Monitoring, Process Control Options
- Process Intelligence Package: Load Cell, LVDT (Linear Variable Displacement Transducer), Touch Screen
- Pressure pad (standard, height sensing, or programmable height sensing) to secure the work piece prior to forming or assembly, to assist with assembly process monitoring / process control, or to confirm part presence prior to continuing the assembly process
Forming Options
- Multi-point or Multi-spindle head for orbital riveting or orbital forming of multiple rivets at the same time
- Static rollerhead for roller forming or roller assembly applications
- Articulating rollerhead for roller forming or roller assembly applications
- Press head powerhead configuration and press tooling to allow the powerhead to act as a press for pressing parts together into any assembly